Fun With Sheathmaking
by Wayne Goddard
There is much more to making a sheath than making it good looking. The way I see it, a sheath has several duties. First and most important, it must protect the owner from the knife. The sheath should also protect the knife from being lost The ideal sheath will also be pleasant to look at and will carry the knife where it is easily accessible.
Making sheaths was the worst part of my first ten years as a knifemaker. I didn’t know what I was doing, and the results showed it. I don’t mind frustrating work, so much if the finished product is something I can be proud of. The sheath for my first knife was riveted together with aircraft rivets found at a surplus store. (See photo) I used the only rivets I thought I could afford. I knew how to use copper harness rivets, but they were too expensive for me. Those early sheaths were not only ugly, but they were not entirely serviceable. I guess it would be better to have an ugly sheath that protected the user from the knife and the knife from loss, than a pretty one that was a disaster waiting to happen.
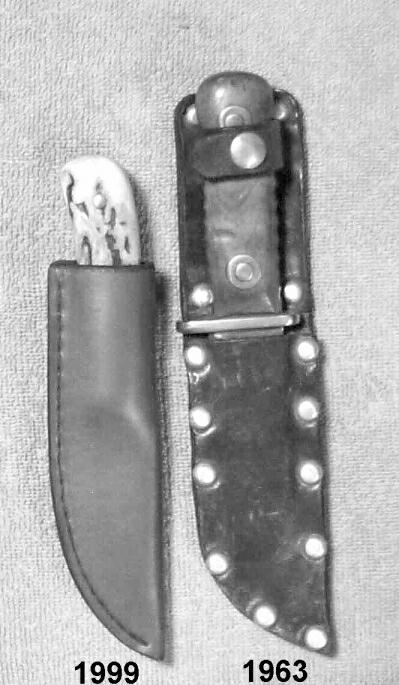
My first clues as to what I was doing wrong came when I found a young saddle maker who was willing to make sheaths for me. I’m not sure he really wanted to make sheaths; but when a craftsman is struggling to get established, whatever work comes in helps pay the bills. I arrived early one day and got to see how he ground and polished the edges of the sheaths. He had already showed me that the lightweight leather I had been using was not adequate for knife sheaths. He moved away after awhile, so I was on my own with my sheath making.
I started using heavier leather and they were finished better, but I didn’t sew any of them. They were all held together with the two-piece “Jiffy” type rivets. Ugly is a good word for those sheaths. It was a few years later that I learned to sew with a hook needle. I had found a different saddle maker who would machine sew my glued up sheaths. One day he offered to show me how to sew with a hook needle. I informed him that I wanted a machine made lock-stitch; a hand-stitched sheath wouldn’t do. He then showed me that sewing with a hook needle makes the exact same stitch that a machine makes. He set me up with a hook needle, and I went home and made myself a stitching horse. That was the last major item in my learning process, I was on my way to working out the total package.
I’ve had many makers look at my sheaths and ask what type machine I used to sew them. They are usually surprised when I tell them it is a hand-sewn lock-stitch.
Most other methods of punching create an irregular line of stitches. To solve this problem, I made a punch out of a reloading press. It makes the holes nice and straight, and that’s what makes the difference in hand stitched sheaths. The hole for a lock-stitch is not punched with a hole punch because the leather would not grip the stitch. The punch for my press is shaped like a tiny bayonet; it spreads the leather without removing any of it. The leather grips the lock-stitch tightly, so even if one stitch got cut, the next stitches would hold tight. Sewing with a hook needle is very fast, once it is mastered.
It was a lot of little tricks and techniques, picked up a piece at a time, that brought me to where I was satisfied with my sheaths. Once I was making great looking and serviceable sheaths what had been a dreaded part of my occupation became a fun finale to the whole package.